Lean Management Implementation: How to Get Started?
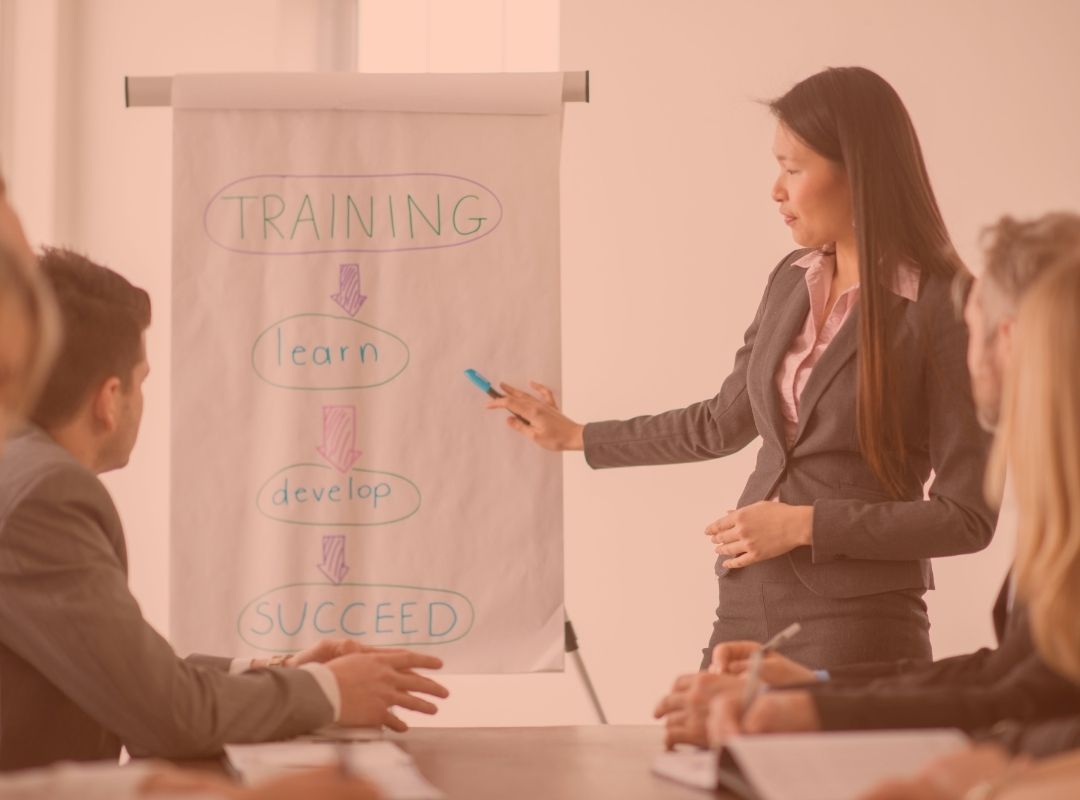
Lean management is an extremely popular management model that can drive serious results for your organization. Lean management is based on the Toyota Production System, which was developed by the the carmaker during the post-World War II era as a way to eliminate waste in the production process while improving productivity and quality. It has since evolved into a practice that’s embraced at some of the world’s largest companies, from Boeing to Intel to Amazon.
But its success relies heavily on how well (or not well) it’s implemented. Which is why understanding lean management principles—and the best practices for implementing this management model in your organization—is a non-negotiable.
Let’s take a look at everything you need to know about lean management implementation—and how to make it work for your business:
What Is Lean Management?
First things first. Before we jump into lean management implementation—and how to embrace it in your organization—let’s quickly define what it is.
“Lean management is a management approach that focuses on streamlining the workflow based on customer needs,” says Felix Lucian Happich, CEO and Founder of strategy consulting firm Felix Happich Consultancy.
It consists of the “building of systems and structures in an organization to deliver the highest value for the customer—while consuming the fewest resources and engaging the entire organization in problem-solving,” says Mark Reich, Senior Coach and Chief Engineer of Strategy at Lean Enterprise Institute and author of the upcoming book, Managing on Purpose.
Or, in other words, this management style attempts to increase value while decreasing unnecessary steps in the day-to-day operations, reducing operational waste—without sacrificing quality or customer service.
What Are Lean Management Principles?
The five principles of lean management are:
- Define value. It doesn’t matter how lean your practices are; if you’re not delivering products or services that your customers actually want, you’re not going to be successful. Which is why defining value—for example, what features are important to your customer? What are they willing to pay extra for?—is a key principle of lean.
- Map the value stream. Value stream mapping involves looking at the entire workflow, breaking down the production products into steps, and then identifying which steps add real value, which can be improved, and which are creating waste—and can be eliminated completely.
- Create flow. Once you’ve eliminated any unnecessary steps in the production process, creating flow is about ensuring each step runs seamlessly into the next without any unnecessary bottlenecks, interruptions, delays, or other issues that would impact efficiency.
- Establish pull. Establishing pull means you only produce what you need, when you need it—which can help eliminate unnecessary inventory.
- Pursue perfection. Once the first four steps are completed, the last principle of lean management is to pursue perfection—or, in other words, optimizing your workflows to eliminate waste and increase efficiency on an ongoing basis.
.png)
There are a number of frameworks that can help you go embrace these principles, like Kanban (which is a visual tool), 5s (which includes 5 steps that all start with the letter “S), or Lean Six Sigma (which has an emphasis on team collaboration)—so you can choose the framework that works best for your organization and team.
What Are The Benefits Of Lean Management?
Lean management offers a variety of benefits—for the company, employees, and customers.
Let’s start with the company. “For the company, the benefits include reduced costs and improved use of resources,” says Happich. “Eliminating unnecessary activities also enhances productivity.”
For example, one study outlined in the Harvard Business Review found that lean projects came in 9 percent under budget and were completed 5 percent faster than other types of projects.
It also offers significant benefits for employees.
“For the teams within the organization, workflows become clearer and [lean management] eliminates inefficiency,” says Happich.
And “by eliminating waste in people’s work, we free people up from tasks that cause them frustration or prevent them from accomplishing their work objectives,” says Reich.
These changes can also increase employee satisfaction. “There is a tendency to improve morale because their time and skills are used more.”
And finally, embracing this management type can ultimately have a positive impact on how customers experience the product and company.
“Customers also experience some benefits,” says Happich. “A more streamlined process means they get the output faster and with improved quality. The business also undergoes continuous improvement to respond to customer needs and eliminate defects.”
Lean Management Implementation: Best Practices To Go Lean
You know what lean management is. You know the benefits it offers, to the company, employees, and customers. Now, let’s jump into the actual implementation process—and the best practices for embracing lean within your organization.
Assess Your Current State
Before you can move forward with implementation, you need to know where your organization currently stands.
“To implement lean management, assessment is important to establish baseline metrics,” says Happich.
Before you start your assessment, think about your goals. What are you trying to do by moving forward with lean management implementation? For example, is your goal to optimize your processes? Improve the customer experience? Save costs?
Once you have your goals in mind, then it’s time to assess your current processes, see how they align with your goals, and identify areas that don’t bring much value and have room to improve. So, how do you do that?
Define what goal-related metrics you’d like to improve using lean management practices—then collect as much data as possible (for example, by using tracking software to understand your current production times or polling customers to get clear customer satisfaction metrics). This will give you a clear starting point, which will help you more accurately measure the success of your lean programs over time. It will also help you identify what areas of your business are struggling the most—which will guide you in what areas to go lean first.
Start With A Pilot Project
Once you assess the current state of your business, you may want to go all-in on implementing more lean programs. But if you’ve been managing your team and operations in a different way, trying to change too many things at once can actually backfire.
“Changes in the organization are usually met with resistance,” says Happich.
Instead, start small. “Start with pilot projects to demonstrate the value of lean management and show why it is necessary for the organization,” says Reich.
Starting with a more simple project—and showing your team what the changes will be like and the benefits it can deliver (including for them!)—can help you generate buy-in and help make a larger scale implementation more smooth.
So, what area of your business should you choose for the pilot project?
“Pick an area in the organization where you know there are important problems that have to be resolved and begin by observing the work and talking to the team that does the work about the problems that exist,” says Reich. “You will learn so much!”
“Then focus your energy on fixing those problems,” Reich continues. According to Reich, once you figure out how to fix the issues in one area, you can take those lessons and apply them to solve problems across the organization—or, in other words, you can scale up your lean management implementation efforts.
Get Leadership Involved
When you implement something new in your business (including going lean!), your team is going to be looking to leadership for guidance on how to move forward—which is why it’s so important to have leaders involved in implementing lean management across the organization.
“Since our topic here is ‘lean management,’ then managers or leaders need to be actively engaged,” says Reich.
So, what does that actually look like? “This means setting up the system to manage but also… actively learning to understand the problems that exist in the value-creating work,” says Reich.
Now, while leaders will need to be involved with implementing lean practices, that doesn’t mean that they have to take everything on themselves. Instead, it’s about getting a hands-on understanding of the systems and processes that are being implemented—so they can then lead and manage their teams more effectively.
“This is different from owning every problem,” says Reich. “It is having an understanding and capability as a leader to effectively coach others to solve the problems you see.”
Also read: How to Train Your Managers to be Better Leaders
Track Progress And Optimize Over Time
Once you successfully roll out your pilot program, it’s time to start implementing lean practices across your organization.
The key to success with lean management implementation is to continually track, evaluate, and optimize your processes—and keep your team in the loop.
“Track progress and share with the team appropriately to keep the process transparent,” says Happich.
For example, if you’re trying to reduce operational waste in your production systems, make sure you’re tracking your production metrics over time. Regularly review the data—and, if needed, make changes to continue to optimize the system and drive more results. Or, let’s say you’re the COO of a consulting company—and you want to improve project management across your organization. In that situation, you might track each of your products (and the activities your team does to manage those projects), see which are the most effective (and why!), and then optimize the rest of your projects to get them up to speed.
Choose the right organizational model for your business
Lean management is a popular management framework—and for good reason! When done well, it can offer a host of benefits for your organization, team, and customers. But it’s not the only model. So before you decide how to move forward in your organization, it’s important to understand the different organizational models and their pros and cons.
Want to learn more about organizational models—and which might be right for your organization? Download our white paper The Ultimate Guide to Organizational Models to discover frameworks like Lean, Agile, and Holacracy, and find out how to implement them in your organization.
Access the White Paper
In our white paper “The Ultimate Guide to Organizational Models,” you’ll receive:
- a comprehensive overview of innovative organizational models (like Agile, Teal, Holacracy, Constitutional Management, and more)
- testimonials from pioneer organizations that have successfully adopted it
- best practices for choosing, implementing and measuring the effectiveness of our model
- digital tools to facilitate your transition
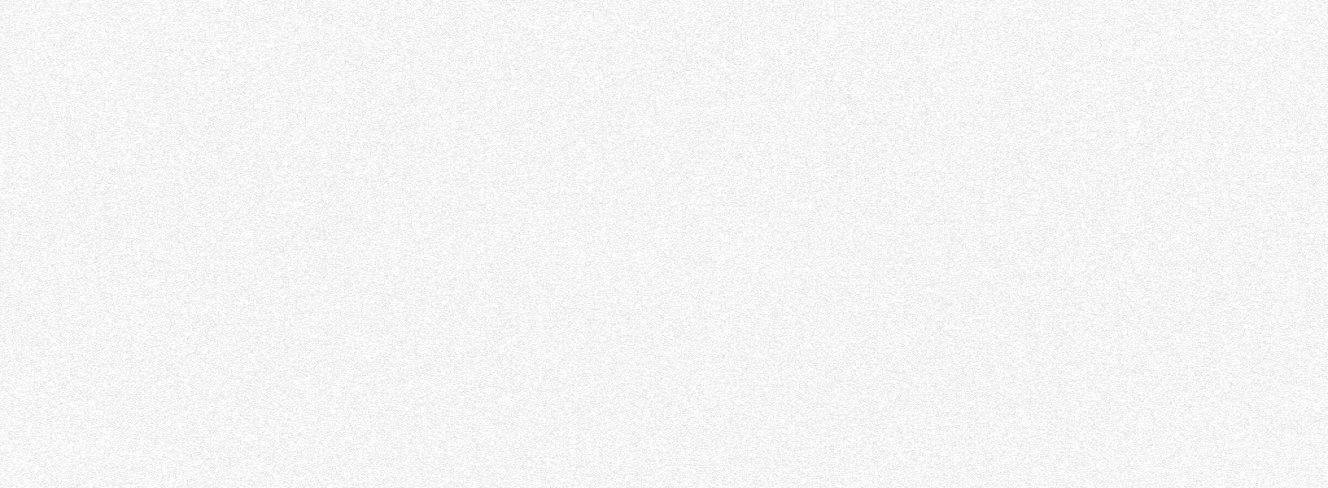